Because they are strong, light, and heat-resistant, ceramics are an incredibly important material for aerospace applications, such as hypersonic jets and space shuttles. That's why 3-D printing ceramics could be useful for companies designing aerospace precision parts like Boeing, Space X, and NASA. Except for one problem: 3-D printed ceramics aren't tough enough to go to space. But a new material design innovation may have just put that problem in the past.
A Malibu, California-based team at HRL Laboratories just announced a new process for 3-D printing ceramics which can resist temperatures up to 1,700 degrees Celsius, or 3,092 degrees Fahrenheit. That's about the temperature experienced by the hottest parts of a NASA space shuttle re-entering Earth's atmosphere after a mission, and a temperature at which most metals turn molten. Amazingly, though, HRL's ceramics may be able to get even hotter without deforming: 1,700 degrees Fahrenheit is just the upper limit on what the researchers were able to test.
3-D printed ceramics aren't anything new, but they tend to stink compared to the real thing. It all has to do with the nature of the 3-D printing process, in which little dabs of base material are melted down and deposited, layer by layer. The problem is that ceramics that are heat-sensitive enough to melt down for 3-D printing printing are, by definition, going to be too heat-sensitive to send into outer space without re-melting.
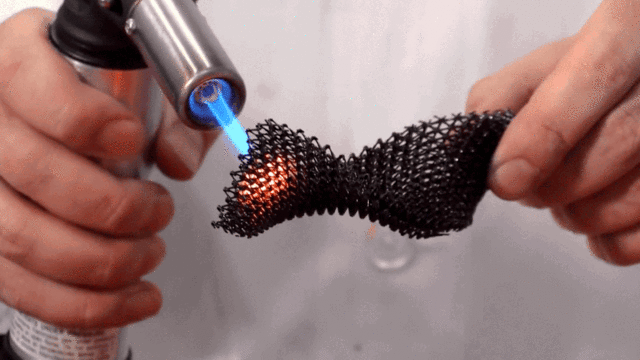
So how'd HRL get around that problem? The team created a type of ceramic which contains a chemical that polymerizes—in other words, permanently bonds—when exposed to UV light. When it's squirted out of the nozzle of a 3-D printer it can easily be melted, but after being baked with UV lamps it hardens, and becomes much less susceptible to heat. Not only can this technique be used to print a staggeringly complex array array of 3-D shapes, but HRL says the resulting ceramics were extremely tough, heat-resistant, and had no surface pores or cracks, even down to sizes only picked up by electron microscopes.
Using this technique, aerospace engineers can now easily 3-D print any weird spaceship part they can think of out of super-strong, lightweight, heat-resistant ceramics. Who knows? The next Space Shuttle might end up being partly contracted from Makerbot.
[via Ars Technica